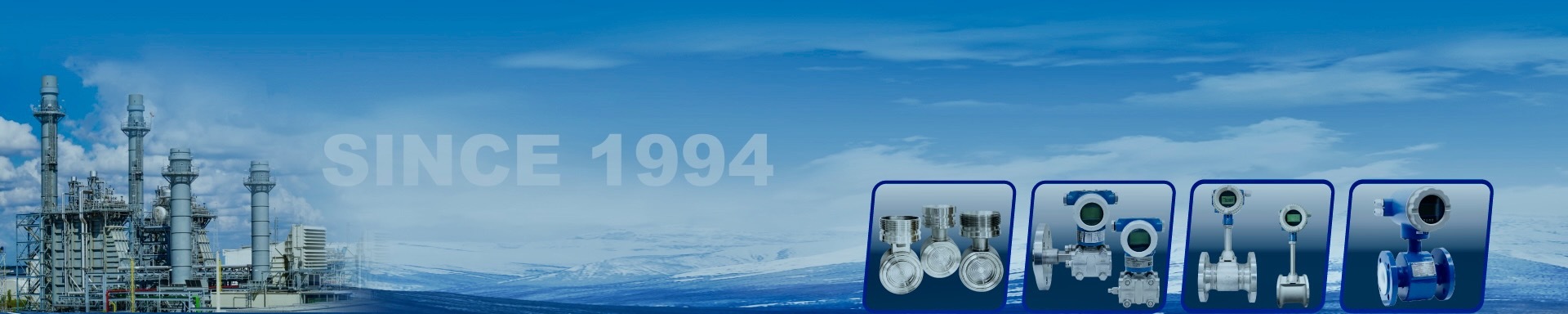
Multi-Angle Analysis And Solution Of Differential Pressure Transmitter Fault
2025-04-14 12:46Fault Model Analysis
In a differential pressure transmitter, the diaphragm is the core component, and its condition directly affects the differential pressure transmitter's performance. When the diaphragm fails, its capacitance changes, which in turn alters the transmitter's output. Analysis shows that variations in the diaphragm's capacitance impact the output, leading to two typical fault conditions. Under normal operation, the output current of the differential pressure transmitter is proportional to the differential pressure and inversely proportional to the diaphragm's elastic modulus. Over long-term use, the transmitter may encounter two common fault conditions: where the differential pressure remains constant but the output current decreases as the elastic modulus increases; where an excessive increase in the diaphragm's elastic modulus results in the output current dropping to zero.
Impact of Diaphragm Failure on the Control Loop
As the transmitter is used over time, the diaphragm's elastic modulus gradually changes. When the elastic modulus increases, the diaphragm's fault coefficient decreases, indicating that its condition is deteriorating. In a simulation study, it was found that diaphragm failure leads to abnormal output currents, which may eventually cause the control system to fail. Under normal circumstances, the differential pressure transmitter's output current maintains a linear relationship with the tracking signal, keeping the entire output process in a stable equilibrium state. However, once the fault coefficient changes, the output current initially increases and then gradually decreases until it eventually reaches zero. Simultaneously, the process variable continues to rise until it reaches its maximum value.
Handling Method and Process
In fault handling, paying close attention to details is crucial. First, the specific type and severity of the fault must be identified and confirmed by observing changes in the transmitter's output current and the process variable's response. Next, based on the fault characteristics, an appropriate solution should be selected, such as replacing the diaphragm, adjusting the elastic modulus, or recalibrating the control loop. During the repair process, it is essential to monitor the control loop closely to ensure that each corrective measure is effective.
AUTO Instrument can provide customized solutions for you. Please let us know your specific requirements — our experience and technology will help solve your problems!